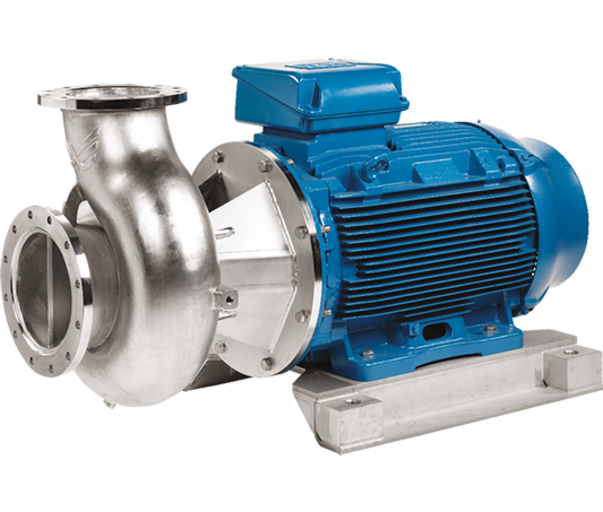
General Industrial Series
The Packo general industrial pump series excel with their high efficiency and low NPSH. The close-coupled modular construction of these pumps uses standardized...
Max. flow | 1800 m3/h |
Differential head | 220 m wC |
The Packo pump range consists of stainless steel centrifugal, lobe and twin screw pumps for hygienic and industrial applications in the food, the pharmaceutical and other general industries. These pumps are built configured to order and tested in our factory in Belgium (Diksmuide). Our pumps rank among the best of the world when it comes to hygiene and cleanability.
Packo is originally researcher, designer and manufacturer of sustainable and innovative hygienic stainless steel centrifugal rotary lobe and twin-screw pumps for various industries.
Our experts can help you with the right pump for your process!
The Packo general industrial pump series excel with their high efficiency and low NPSH. The close-coupled modular construction of these pumps uses standardized...
Max. flow | 1800 m3/h |
Differential head | 220 m wC |
The Packo sanitary pump series are designed for use in the most demanding hygienic applications in almost all industries such as dairies, breweries, beverage industry, distilleries, etc. They are the ideal solution for filtration applications, pasteurisation, evaporating systems, yeast propagation and for CIP cleaning systems as well.
Max. flow | 1800 m3/h |
Differential head | 220 m wC |
Each series of the Packo rotary lobe pumps is, in its field, a state-of-the-art. The pumps can be fitted with a variety of features and rotors to adapt to almost all hygienic pumping tasks. The pumps can be customized for an optimum function or performance to your process.
Max. flow | 1670 l/min |
Max. discharge pressure | 20 bar |
The Packo ZLC lobe pump pharmaceutical process pump is 3A certified. These perfectly cleanable pumps can be applied in the most demanding sterile applications in the...
Max. flow | 1666 l/min |
Max. discharge pressure | 20 bar |
Standard surface finish: 0.8µm (150 grit), with 0.5µ (240 grit) and electropolish options. Optional steam/sterile fluid barriers on joints and front cover sealing, for true aseptic processes. High efficiency to minimise damage to shear-sensitive low viscosity fluids.
Max. flow | 44m³/hr (12 litres/second) |
Max. discharge pressure | 20bar (290 psi) |
Hy~Line Rotary Lobe pumps are robust, durable pumps designed for long life in demanding applications.
Max. flow | 131m³/hr (36.6 litres/second) |
Max. discharge pressure | 15bar (220 psi) |
The Hy~Line LT range of truck mounted pumps are used for the loading and unloading of a wide variety of products.
Max. flow | 684 L/M (lpm) |
Max. discharge pressure | 15 bar |
During red winemaking process, 4~5 days fermentation and 30~40 days maceration is needed. The process of fermentation in wine is the catalyst function that turns grape...
Max. flow | 300 l/min |
Max. discharge pressure | 6 bar |
Every feature on the ZP range has been specifically designed to make dismantling (whether for inspection, cleaning, or maintenance) quicker, easier and cheaper. What’s...
Max. flow | 708 l/min |
Max. discharge pressure | 15 bar |
All advantages of rotary lobe and centrifugal pumps are combined in the Packo twin screw series. This two-in-one pump is excellent for pumping high viscous liquids & pastes but also the thin-liquid cleaning fluids that are used for CIP cleaning. Pulsation free for gentle operation.
Max. flow | 1660 l/min |
Max. discharge pressure | 12 bar |
Write down the serial number of your pump and give us a call! We're always happy to help you.
Please allow 5 working days delivery time for our products.
Our pumps are manufactured in Belgium.
Whether it is about hygiene, cleanability, wear- or corrosion resistance, for each of these challenges Packo offers a solution. The possibilities are almost endless. Today you find us back in breweries, chemical and cosmetics industries, animal feed, pharmaceutical industry, agro-industry but also in the dairy industry, textile- and fish world.
This can have several causes.
First, it must be checked that the pump is running in the right direction as indicated on the nameplate and manual. A centrifugal pump that turns in the wrong direction takes a lot of motor power, but delivers almost no flow. In addition, the capacity of the pump also depends on the speed of the pump. For the remainder of this explanation, we assume that the direction of rotation and speed are correct.
The flow that a centrifugal pump delivers, is always a balance between what the pump can do and what the pipework connected to the pump allows. The pressure that a centrifugal pump (at a fixed speed) creates, will decrease slightly with the flow rate, but it is quite constant all in all. However, to push a larger flow through a pipe work, more and more pressure is needed. This necessary pressure consists partly of a static height difference (you want to use the pump to pump the liquid from low to high) and partly of friction losses. The static height difference is independent of the pumped flow, the friction losses with centrifugal pumps (which pump low viscous liquids) are usually quadratically proportional to the flow. So to pump twice the flow through a pipework, the pump has to press 4 times as hard, so 4 times more head is needed.
When pumps deliver less flow than expected and than indicated on the pump nameplate, in practice the pump usually delivers the pressure indicated on the nameplate, but not the desired flow rate. The cause for this is not caused by the pump, but by an incorrect estimate of the friction losses. In other words: the pump delivers the expected pressure, but the pipework allows less flow at this pressure. In order to be able to pump the desired flow through the pipework, the pump would have to press harder, in other words more pressure is needed; requires more pressure than indicated on the pump nameplate. In other words, the pump delivers the pressure expected, but more pressure is needed to push the desired flow through the pipework.
There are 2 possible reasons why a pump does not deliver the indicated pressure:
- Either the pumped liquid is gaseous. Due to the gas phase in the liquid, the average specific gravity ρ is lower than that of water and the formula ρ * g * h produces a lower pressure. At higher gas concentrations, even a gas bubble collects in the impeller eye and the pump delivers even less pressure.
- Either the pump is cavitating. Cavitation also collects a gas bubble in the impeller of the pump.
In centrifugal pumps, the pressure is generated by centrifugal forces. These are themselves generated by the rapid rotation of the liquid in the pump casing. Centrifugal pumps therefore require speed to generate pressure. The greater the pressure required, the greater the internal fluid velocity in the pump.
Viscosity creates friction in the fluid located between the impeller and the pump casing. This fluid friction creates resistance to spinning. So power is needed to overcome this friction. An increasing viscosity therefore increases the power consumption of the pump. This increase is all the faster at high speeds or therefore with pumps that have to deliver a high pressure. The impact of the viscosity on the power of centrifugal pumps delivering low pressure is smaller. Therefore, a centrifugal pump is not a good choice for generating high pressures with highly viscous liquids.
With lobe pumps and screw spindle pumps, there is always a small play between the rotors and between the rotors and the pump casing. In order to make the pump as efficient as possible, these clearances are kept as small as possible, but to prevent the rotors from running into each other or in the pump casing, they are always present. These clearances form an open connection between the outlet and the inlet of the pump. With thin viscous liquids, these clearances between the rotors and between the rotors and the pump casing create an internal leak: some liquid is forced from the outlet of the pump (where there is a higher pressure) through this narrow passage back to the inlet. (where there is a lower pressure). This internal leakage rate increases as the viscosity of the pumped liquid decreases. Therefore, volumetric pumps are less efficient with low viscous liquids.
The question now arises as to which viscosity a centrifugal pump is the better choice and from which viscosity it is better to choose a volumetric pump. The answer to this question is that it depends not only on the viscosity, but also on the required head and flow. So you cannot give a fixed viscosity value where it is better to switch from centrifugal to volumetric. With a high pressure head and a small flow rate, switching is better at a lower viscosity, while at a high flow rate with a low pressure head you can stay longer with a centrifugal pump. The example below should make this clear.
When selecting a pump for 5 m³/h - 4 bar pressure, even with water (viscosity 1cP) less power is required with a rotary lobe pump than with a centrifugal pump.
When selecting a pump for 40 m³/h - 1 bar pressure, a centrifugal pump still requires less power than a volumetric pump, even at a viscosity of 1,000 cP.
In addition to the necessary power, the initial cost and maintenance costs also play a role in the choice of pump technology.
Shear is the difference in speed between 2 layers in the liquid. The degree of the shear is expressed by the shear rate, which represents the velocity gradient in the liquid. When 2 layers of liquid that are 1m apart have a speed difference of 1 m/s, then there is a shear rate of 1/s in the liquid between these 2 layers.
As soon as a liquid is in motion, shear is created. The velocity is never the same for each liquid droplet, so there is always a relative movement of one droplet versus the other, thus creating shear. Even with so-called plug flow, shear will form on the wall because this wall is stationary or moves faster than the liquid and thus slows down or entrains the liquid.
In pumps, there are moving parts as well as stationary housing. In view of the small distance between the moving parts and the housing, a large velocity gradient or high shear rate will develop in the fluid between them. The flow will also cause shear in the supply and discharge pipes, albeit a lower one.
Shear cannot be avoided and is not a problem in itself. Sometimes a high degree of shear is even desirable. For example, in a high-shear pump a high shear rate is generated to form emulsions or dispersions, or in general, to mix liquids that are difficult to dissolve into each other more or less stably.
However, the impact of shear on the microstructure of a fluid is not always positive or desirable. Shear, for example, can also damage sensitive liquids. Due to the shear stress between the liquid particles, an impact on the viscosity of the liquid is also seen in many complex liquids.
Liquids whose viscosity is not influenced by the shear rate are called Newtonian liquids. They are typically chemically simple liquids: water, oil, sugar solutions, ...
With much more complex liquids (preparations), the viscosity will decrease as the shear rate increases. These liquids are called thixotropic. As soon as the shear rate decreases, the viscosity increases again. The shear does not destroy the liquid structure and will not change it permanently. This means that a thixotropic liquid has the highest viscosity in a tank where it is at rest, so no shear. Due to the shear created by flow through a pipe, the viscosity decreases. In a pump, where the shear rate is much higher, the viscosity is at its lowest. When the liquid leaves the pump, the viscosity recovers as the shear rate falls back.
With a small group of liquids, the viscosity actually increases with a higher shear rate. These liquids are called dilutant. Examples of dilatant liquids are honey and concentrated starch solutions. Due to their dilatant behaviour these liquids are very difficult to pump.
The influence of the shear rate on the viscosity of these three types of liquids is shown graphically here:
The pump curve of a centrifugal pump gives the head, the absorbed power, the efficiency and the NPSH in function of the flow at a fixed speed. Usually the pump curve is published for water, or even: for a liquid with a specific weight of 1 kg / liter and a viscosity of 1 centipoise.
With centrifugal pumps there is a formula to convert the pump curve from one speed to another:
- Flow is directly proportional to speed
- Head and NPSH are quadratically proportional to speed
- Power input is proportional to speed to the power of three
- Efficiency is independent of speed
A lobe pump is a volumetric pump and therefore the flow rate delivered and the required power are initially directly proportional to the speed. This is also the case with highly viscous liquids and you can easily state that the flow and power vary linearly with the speed. The flow is the so-called stroke volume of the pump multiplied by the speed of the pump. The stroke volume of a rotary lobe pump is the volume of liquid that is moved per revolution of the rotors from the suction to the discharge of the pump.
However, with thin-viscosity liquids, leakage occurs between the rotors and between the rotors and the rotor casing, causing the pump to deliver less flow. Before explaining the influence of speed on the pump curve with thin-viscosity liquids, we will first discuss the construction of the pump curve with water as an example.
Per revolution, the pump initially moves the volume of water from the suction to the press again. However, under the influence of the pressure difference over the pump, a certain amount of water continuously flows back from the press (where there is a higher pressure) to the suction of the pump (where there is a lower pressure). This leakage flow rate is proportional to the square root of the pressure difference across the pump. So with a small pressure difference across the pump, this leakage flow rate will be small and most likely smaller than the flow rate of water the pump displaces through its rotation (the higher explained stroke volume * speed). Net, the pump still pumps water from the suction to the press.
If the pressure difference across the pump becomes large, the leakage rate can exceed the volume the pump moves through the rotation and eventually net water flows from the press to the suction of the pump. In the graph shown here this is the case with a pressure difference greater than 7.5 bar.
The leakage rate is independent of the speed. So if we increase the speed, then:
- the flow we transfer from the suction to the press through the rotation will increase linearly with the speed
- the leakage rate will remain the same
Since the net flow the pump pumps is the difference between the two, the pump curves will shift upwards in parallel with increasing speed. You can see that visualized here.
Starting in 1975, has designed and constructed stainless steel pumps for various industries with a focus on machine builders. Since this date, we have supplied more than 350,000 pumps and these for the most diverse applications.
The first pumps that were developed by us were destined for the dairy industry, so from the outset hygiene and cleanability were a basic requirement for Packo pumps.
The use of stainless steel and the standard applying of an electrochemical surface treatment (electropolishing), find their origin here. These are two factors that make Packo pumps stand out even today. Diversification and deepening of knowledge have led to Packo being a market leader in various sectors today.
Since the summer of 2015 Packo belongs to the Verder group. Together we employ 2000 people worldwide spread over different production sites and sales offices. In the factory in Diksmuide we manufacture industrial pumps and hygienic components. There is also an electropolishing division which gives our products a very high degree of finish.
Packo is creating the highest quality hygienic and sanitary pumps for industrial, food and pharmaceutical applications. The centrifugal pumps are manufactured in Belgium. All centrifugal pumps are electropolished according to an in-house developed process method for surface treatment of stainless steel.
The method is finished with hand polishing techniques to achieve the highest quality pump specification for applications where compromise is not an option. Started in 1975 with dairy pumps, Packo Pumps has developed its portfolio to include models for many certified processes including FDA, 3A and EC1935/2004. The rotary lobe pumps and twin-screw pumps are manufactured in South Korea.
With a dedicated team and investment in advancing technology, Verder can offer its Packo pumps as a premium option for compliant applications. The Diksmuide plant produces not only pumps but also static and dynamic mixers.
The hygienic pumps from Verder are problem solvers for the hygienic market. The Packo centrifugal pump series can meet the high requirements of EHEDG and 3A certification. They excel in hygienic cleanability, reliability and are easy to handle. All Packo centrifugal pumps are configured to order, offering a huge range of pump configurations. The standard pumps are used in demanding applications such as dairy, food & beverage and pharmaceutical. This series is also perfectly applicable in industrial applications such as mining, chemicals and waste water. In fact at all duties where a high corrosion resistance is required.
Each series of the Packo rotary lobe and circumferential piston pumps is stateof-the-art. The pumps can be fitted with a variety of features and rotors to adapt to almost all hygienic pumping tasks. The pumps can be customized to meet the optimum function or performance to your process.
All advantages of rotary lobe pumps and centrifugal pumps are combined in the Packo twin screw series. This two-in-one operation pump series is excellent for pumping not only high-viscous liquids and pastes but also the thin-liquid cleaning fluids that are used for CIP cleaning. The pumps provide a pulsation free flow for gentle operation.
In May 2021 Verder added the Jabsco lobe pumps to the offering of Verder Liquids into the hygienic market by acquiring the Jabsco lobe pumps from Xylem. Jabsco is a very well-known and established name in the market with a highly loyal customer base and adding the lobe pump product line will fortify our position as a hygienic pump specialist.” All Jabsco lobe pumps can be purchased from the Verder organization under the Packo brand. All other Jabsco product lines and technologies are being retained by Xylem, which continues to serve multiple industrial sectors.