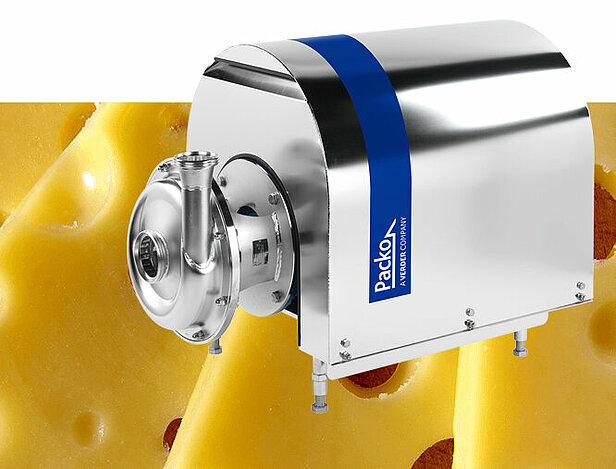
Eet uw pomp ook de kaas van uw brood
Opmerking: deze casestudy is alleen van toepassing op harde kazen
Er bestaan een aantal hardnekkige vooroordelen over wat de juiste pomp is in een productieproces van harde kaas. Als deze vooroordelen niet kloppen, halen kaasproducenten niet het maximale uit hun proces. Dit geldt zowel voor de efficiëntie van het proces als voor de kwaliteit van het product.
Daarom hebben we onderzocht of deze vooroordelen een kern van waarheid bevatten en dit in samenwerking met een producent van Emmentaler kazen.
Tegelijkertijd hebben we geprobeerd een veelvoorkomend probleem in het productieproces van harde kazen op te lossen. Bij de productie van harde kazen ontstaat vaak een ongewenst bijproduct, namelijk wrongelfijn.
Dit bijproduct wordt bij voorkeur vermeden omdat het een negatief effect heeft op de kwaliteit van de kaas en dus op het rendement van de kaasproducent. Het punt is: hoe meer van dit bijproduct (wrongel) wordt geproduceerd, hoe minder van het hoofdproduct (de kaas zelf) overblijft.
Een van de belangrijkste redenen voor de vorming van wrongel is het te ruw pompen van het product. Geen wonder dus dat de keuze van de pomp een grote rol speelt bij het voorkomen van wrongelvorming.
Aan de hand van een concreet praktijkvoorbeeld willen we laten zien hoe een juiste pompkeuze dit probleem oplost en tegelijkertijd de kwaliteit en efficiëntie van het proces verhoogt.
Huidige visie op de markt
Momenteel zijn er ongeveer 4 verschillende soorten pompen in het productieproces voor harde kazen:
- Monotype pomp
- Sinuspomp
- Lobbenpomp
- Vortexpomp (centrifugaalpomp met vortexwaaier)
Over het algemeen wordt aangenomen dat vortexpompen en lobbenpompen de beste pompen zijn om wrongelfijnheid te voorkomen. Laten we deze 2 soorten pompen eens nader bekijken.
Ten eerste, lobbenpompen. Deze hebben het voordeel dat ze langzaam draaien en weinig schade aanrichten, maar het nadeel is dat ze vrij duur zijn (vooral voor grote debieten hoger dan 50 m³/h). Bovendien hebben ze zelfs een aparte CIP-pomp nodig (CIP = cleaning in place).
Ten tweede zijn er de vortexpompen, dit is een type centrifugaalpomp met een teruggetrokken waaier (vortexwaaier) die rechte schoepen heeft en een pomphuis dat volledig rond is (Figuur 1).
Er wordt aangenomen dat de verzonken waaier ervoor zorgt dat de wrongel niet "door" de waaier gaat en daardoor minder schade aanricht dan een gewone waaier.
Maar kloppen deze aannames wel of zijn het vooroordelen?
Mogelijke alternatieven?
Is een vortexpomp echt de beste oplossing voor dit probleem? Bij het benaderen van deze vraag hielden we het volgende in gedachten:
"Een pomp met een zo hoog mogelijk rendement zorgt voor een soepeler verpompen van het medium en dus voor minder schade aan de wrongel."
Om tot een alternatief te komen, gebruikten we ons CFD-systeem (= Computational Fluid Dynamics). Deze software maakt het mogelijk om het medium in de pomp te simuleren. Dit gaf ons de mogelijkheid om de volgende punten te verbeteren:
- De turbulentie verminderen;
- De efficiëntie verhogen
- Wat zal resulteren in een algemeen zachter pompen van het medium.
Deze studie leidde ons naar een Packo-pomp met de volgende kenmerken:
- Pomp met hoog rendement;
- Pomphuis met voluutvorm;
- Gesloten waaier met 3D-schoepen.
In een volgende stap vergeleken we onze oplossing met de gebruikelijke vortexpomp en die op hetzelfde werkpunt: 60 m³/h op 7m. Dit leverde het volgende resultaat op:
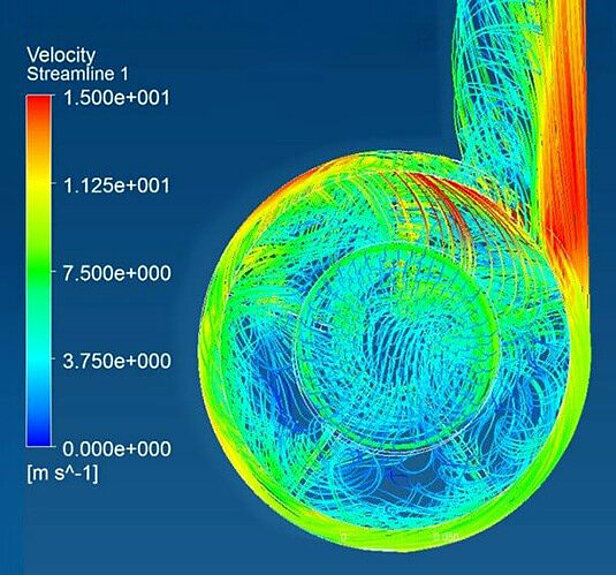
Vortex-waaier
- Snelheden > 15 m/s
- Dode zones
- Grote variatie in snelheid
- Efficiëntie: 58%
⇒ Brusque pompen
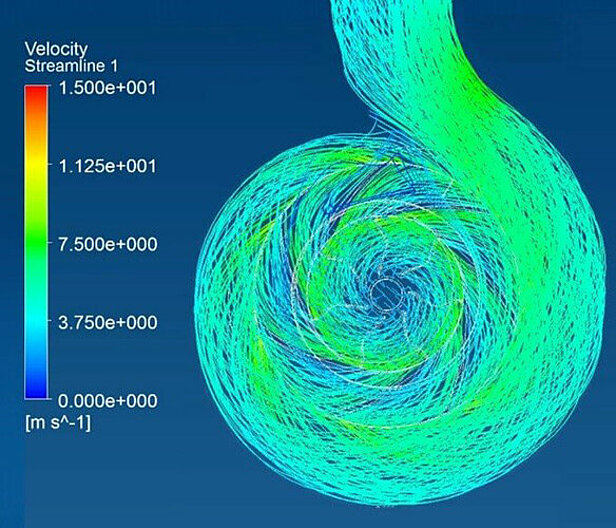
Gesloten waaier
- Snelheden < 7 m/s
- Geen dode zones
- Kleine snelheidsvariatie in de pomp
- Rendement: 75%
⇒ Zacht pompen
Wat dus snel duidelijk werd uit deze test is dat een gesloten waaier een hoger rendement haalt dan de vaak gebruikte vortex waaier.
In het standaardgamma van Packo hebben we 2 pompen die aan deze karakteristieken voldoen, de FP3 en MFP3. Deze pompen konden dus gebruikt worden voor onze test bij de klant.
In de praktijk
Voor dit onderzoek hebben we nauw samengewerkt met een klant die Emmentaler kaas produceert. Zoals de meeste kaasproducenten gebruikten ook zij vortexpompen in hun productieproces.
Voordat de test met Packo werd uitgevoerd, had de klant zelf al een aantal dingen uitgeprobeerd:
- Een lagere en hogere snelheid van de pomp instellen;
- Langere en kortere vultijd ingesteld;
- Verschillende druk aan de vulmond (0,25 - 0,5 bar);
- Vulmondstuk met verschillende diameters (17 - 22 mm).
Al deze aanpassingen lieten geen duidelijke verbeteringen zien zoals verwacht, in sommige gevallen werd een vermindering van de kwaliteit waargenomen. Een mindere kwaliteit van de kaas is ook merkbaar aan de volgende kenmerken:
- Aanwezigheid van wrongelbobbeltjes op verschillende plaatsen aan het oppervlak, waardoor problemen ontstaan tijdens het persen van de jonge kaas met de scheiding van vaste fase (wrongel) en vloeibare fase (wei);
- Ongelijkmatige vulling van de vorm;
- Kaasrondjes die in het midden dunner zijn dan aan de buitenkant;
- Kaasrondjes met verschillend gewicht;
- barsten in de kaas.
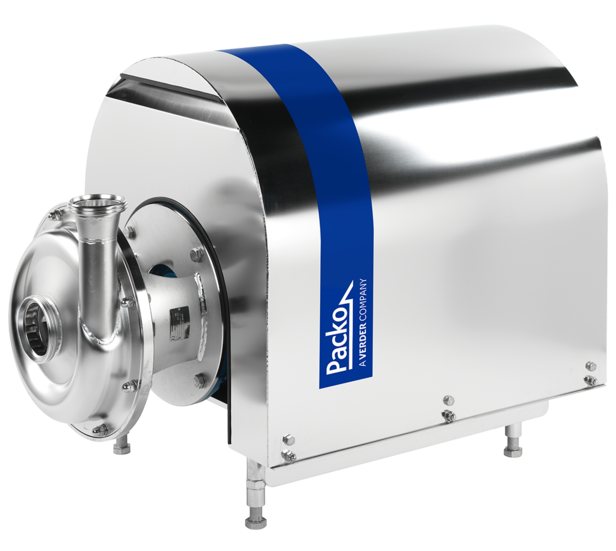
Onderzoeksdoelen
Om van een succesvolle oefening te kunnen spreken, had onze klant de volgende doelen gesteld:
- Vultijd van de kaasvorm ongeveer 12-13 min;
- De druk op de vulmond (dispenser) is altijd tussen 0,30-0,35 bar;
- Gelijke verdeling van de wrongel in de verschillende kaasrondes (6, 8 & 10);
- Geen wrongel fijn;
- Hetzelfde gewicht voor alle kaasrondes (ca. +/-3kg);
- Consistente vulling (symmetrisch);
- Kwaliteit van de kaas voldoet aan de eisen van de markt (aantal gaten, duurzaamheid & houdbaarheid).
Praktijktest systeemparameters
Ondertussen werd de volledige installatie bij de klant geëvalueerd. Om te bepalen welke pomp en onder welke omstandigheden het beste resultaat zou opleveren. Om zo een optimale selectie te kunnen maken.
- Beoogd werkpunt: 60m³/h @8,6m.
- Pompkeuze een Packo FP3/100-250 pomp met de volgende karakteristieken:
- Motor van 5,5kW - 6-polig (1000 tpm => 700 tpm);
- Gesloten waaier;
- pompefficiëntie van ongeveer 75% op het werkpunt.
Deze pomp werd gebruikt in het productieproces in de kaasfabriek en onderworpen aan verschillende tests om de optimale instellingen te onderzoeken. Dit is nodig omdat er verschillende soorten kaas worden gebruikt (6/8/10) die verschillende snelheden en werkpunten vereisen.
Hieronder vindt u een overzicht van de instellingen die zijn getest en wat de uiteindelijke resultaten zijn geworden.
Testfase | Definitieve instelling | |
Druk bij de dispenser |
0.1 – 0.6 bar |
0.30 – 0.35 bar |
Vultijd |
9-13 minuten |
12 minuten |
Pompsnelheid | Verschillende snelheden | 600 tot 700 RPM |
Heeft de pomp het goed gedaan?
Nu blijft het belangrijkste over. Toonde de test positieve resultaten bij de klant?
Na het invoeren van de FP3 pomp in het productieproces zagen we de volgende resultaten:
- Geen verliezen meer als gevolg van wrongelfijnheid;
- Symmetrische kazen;
- Hetzelfde gewicht aan kaas bij de productie van de verschillende kaasrondes (6, 8 & 10);
- Kwaliteit van de kaas voldoet aan de eisen van de markt (aantal gaten, duurzaamheid & houdbaarheid;
- Zeer laag geluidsniveau tijdens het pompen van de wrongel
- Sterker nog, al deze veranderingen zorgden ervoor dat de pomp zichzelf na 3 (!) maanden had terugbetaald.
Een goede pompkeuze had dus een positieve invloed op het hele productieproces: van de efficiëntie van het proces tot de kwaliteit van de kazen zelf.
Neem contact met ons op en we bewijzen dit ook voor uw proces.